Plastics Recycling for Direct Food Contact and Alternative Applications
Plastics are among the materials most widely used for food contact applications. While there is pressure to use recycled plastics in packaging in order to combat plastic waste, certain conditions must be met before food packaging can be considered safe.
The criteria for what is commonly referred to as “food safe” essentially aim to ensure that substances are not be transferred from the packaging to the food in quantities that could endanger consumer health. The composition of the food must remain unchanged and its quality in terms of taste and aroma must not be impaired. Because food packaging is also sometimes misused as a container for various other substances before it is disposed of, this presents additional challenges in the process for producing recyclates intended for direct food contact applications.
The route to obtaining a safety evaluation of recycling processes for the production of recyclates for direct food contact is via the European Food and Safety Authority (efsa) in the European Union and via the Food and Drug Administration (FDA) in the USA. The evaluation itself is largely dependent on the substance to be packaged, the polymer in contact with it and storage parameters such as time and temperature. Polyethylene terephthalate (PET) is an inert polymer and PET bottle-to-bottle recycling has been established for more than 20 years. High-Density polyethylene (HDPE) on the other hand is more permeable and less dense. The requirements for ensuring the safe reuse of HDPE milk bottles, for example, are therefore much stricter and more comprehensive, from checking returned bottles to the recycling process. How strict and comprehensive is determined by the different evaluation criteria specified by the efsa and FDA.
PCR-HDPE for Direct Food Contact
EREMA received confirmation from the FDA in autumn 2019 that HDPE produced using up to 100% post consumer recycling (PCR-HDPE) with the patented Intarema TVEplus RegrindPro extrusion system in combination with the ReFresher module is suitable for use in food packaging. The starting material is a defined input consisting 99 % of food contact compliant HDPE packaging, e. g. milk and juice bottles. The PCR-HDPE recycled this way can be reprocessed into bottles, but also into food cups and disposable dishes and cutlery. In its no-objection letter, the FDA states that the recycling process reduces potential contaminants to such an extent that they do not enter the food in concentrations higher than 0.5 ppb. This is the limit set by the FDA for classification as a negligible risk to consumers. The conditions to be met apply to the refrigerated storage of milk, juice and meat products packed using the recycled material. In addition, disposable dishes and cutlery produced from it may only come into contact with cold and hot food for a short time.
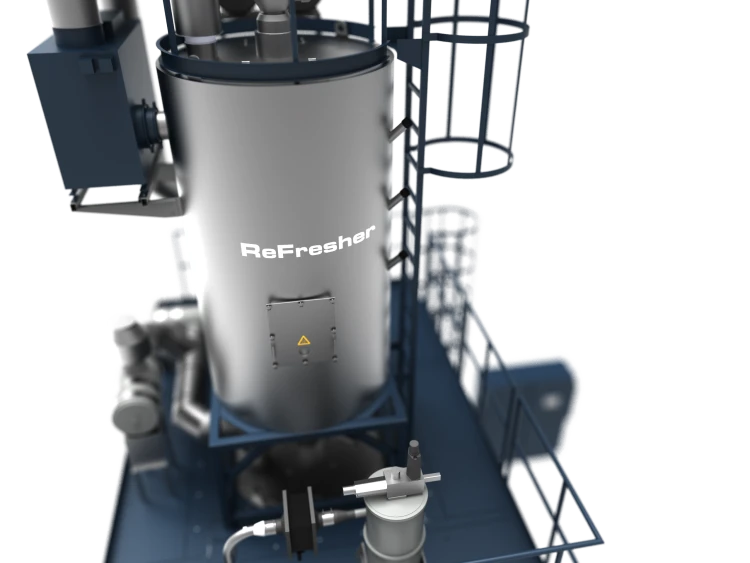
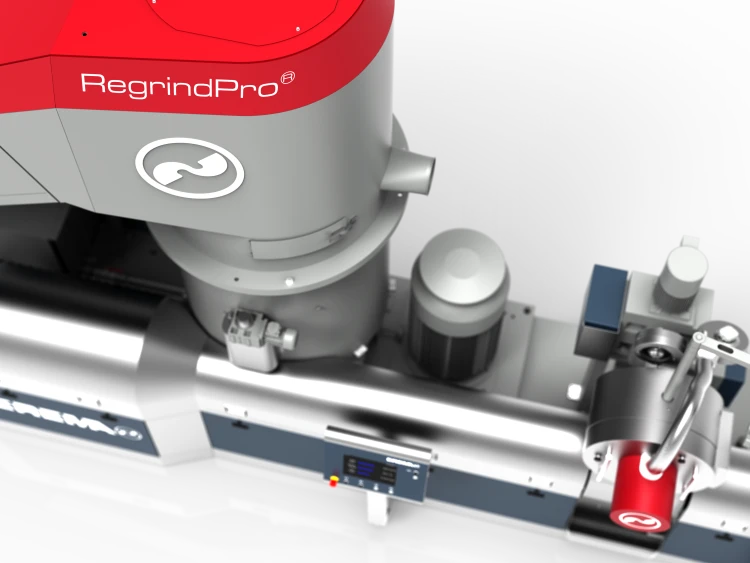
For this assessment, the cleaning efficiency of the HDPE recycling process was subjected to what is referred to as a challenge test. 150 kg (331 lb) of sorted and washed HDPE flakes from the yellow bag contaminated especially for the test were recycled. A worst-case scenario was created for the contamination of the flakes, both in terms of the quantity of the substances applied and the duration of the contact with contaminants. The test proved that the concentration of highly volatile substances (toluene, chloroben-zene) was reduced to values below the analytical detection limit during the recycling process. The concentration of methyl salicylate and the low-volatility compound benzophenone was also significantly reduced in the recycled product, as was the concentration of the oligomers typical for HDPE. With one exception (methyl stearate, which has a particularly low volatility), the cleaning efficiency was over 99%.
FDA approval opens up new opportunities for EREMA’s customers who are active within the US market and countries with FDA regulations. By comparison, PCR-HDPE extracted from milk bottles has been used again in the production of milk bottles in the UK using EREMA recycling technology (Vacurema) since 2008, but only in proportions of up to 30% (although FDA approval for this would permit proportions of up to 50%). With the recycling technology described, this proportion could now be increased to up to 100%.
Alternative Use in Cosmetics Packaging
This explains why the EU is seeing increased use of PCR-HDPE in alternative end products that are also of a very high quality. Take for example the world’s first shower gel bottle made of 100% PCR- HDPE by Werner & Mertz – launched in Germany in the spring of 2019. This is remarkable because – in order to be considered safe – cosmetic products also have to meet very high requirements regarding contamination caused by migration from the packaging (EU regulation on cosmetic products (EC) No. 1223/ 2009). And that has been achieved by recycling HDPE hollow bodies from the yellow bag. After sorting and a special wash- ing process, the flakes are recycled by the Intarema TVEplus RegrindPro plus ReFresher module, for which EREMA has received FDA confirmation.
Featuring ReFresher technology, the system decontaminates the material and eliminates odors. Thanks to the high quality of the PCR-HDPE obtained this way, many sensitive applications can be considered for this input material, including body care products, for example. However, more and more manufacturers are turning to PET or rPET for precisely this purpose. As a result, if rPET suitable for food contact is used to make shower gel bottles, it loses this suitability as a consequence and can no longer enter the cycle for direct food contact material. A separate collection system for non-food rPET would therefore have to be created if it is to be used again.
rPET for Direct Food Contact
Because PET is an inert material, the risk of migration is significantly lower, which is why PET recycling processes and recyclates also meet the particularly stringent efsa requirements. To date, efsa has published more than 140 statements on PET recycling processes – all of them positive. In the EU, national directives and several EU regulations are currently used to assess food contact compliance (see Box). The EU plans to allow only recycling processes that have been evaluated by the efsa and approved by the European Commission (DG Sante) for the production of food packaging that is made partly or completely using recycled plastic.
The recycling plant operator has to apply for authorization as a prerequisite for an assessment.
So far, the efsa has issued and published statements on the safety assessment of PET recycling (bottle-to-bottle, bottle-to-sheet, bottle-to-tray), including numerous processes involving EREMA’s bottle-to-bottle technology. Although all the PET recycling processes they assessed have been evaluated positively, there is still no official approval or authorization. A decision from the European Commission is still pending, after which they will publish a list of the processes that have been approved.
At present, the national authorities are informed and trained using what is known as the CMSS (compliance monitoring summary sheet), so that they can also audit each recycling plant operator following official authorization. Once this has been done, recycled plastics intended for direct food contact may only be produced using the listed processes. Until then, the EU directives and national laws mentioned above will continue to apply, and recycling plant operators can have their compliance with these regulations checked and certified. However, official approval of the processes based on accepted and binding quality criteria is urgently needed to provide the industry with legal security. This final decision has been pending since the introduction of the EU regulation (EC, No. 282/2008) twelve years ago.
EU Regulations
The following regulations are used for the evaluation of food contact compliance: regulation on materials intended to come into contact with food (EC No. 1935/2004), regulation on good manufacturing practice (EC No. 2023/2006) and a legal directive specifically for plastics used in food contact materials (EU, No. 10/2011). This establishes an overall migration limit and includes a binding list of monomers and additives authorized for the production of food contact materials, together with each of their specific migration limits. These limits are based on the assumption that a person weighing 60kg (132lb) consumes 1kg (2.2lb) of food packaged in plastic containing the substance in question at the maximum permitted quantity every day for the rest of their life.
Originally appeared in "Kunststoff international", May 2020
(article, 20.05.2020)