Screws, spindles and spirals are core parts in the extrusion industry and 3S GmbH, a member of the EREMA Group, is not only considered an innovative producer of these parts, but also an expert in wear protection, repair and regeneration. At K 2022, the company will demonstrate at the EREMA Group stand how a new type of cylinder enables ultrasonic wear measurements, and a new screw manufacturing technology leads to more efficient production.
What began in 1992 at the company's Roitham site in Austria proves to be a 3-decade success story in 2022, the year of the company's 30th anniversary: During this time, 3S has established itself worldwide as a leader in the production of quality core parts for the extrusion industry. In producing these parts for the plastics, rubber, chemical, oilfield and food industries as well as for ceramic extrusion, the company generated sales of around EUR 25 million in financial year 2021/22 with 115 employees at two locations. The focus continues to be on the manufacture of extruder screws for plastics and recycling technologies. Between 1,500 and 2,000 screw and cylinder orders are currently processed every year - with a strong upward trend. The company also manufactures screens for EREMA laser filters using a patented laser process. The company is preparing for the growing demand with an unprecedented programme of investment. 25 percent of turnover will be invested in the expansion of production halls and new manufacturing equipment at both sites.
Wear measurement without machine downtime
At K 2022, 3S will present a new type of cylinder that enables ultrasonic wear measurement of the extrusion screw and cylinder while the machine is running. "This saves the customer from having to shut down and restart the plant, remove and reinstall these parts, and clean and measure them, which would usually mean one to two days of machine downtime," explains Alois Anreiter, CEO at 3S. With developments like this, the company is also supporting the implementation of new digitalisation solutions for recycling systems at the EREMA Group. These are aimed at making machine data usable for increasing machine performance.
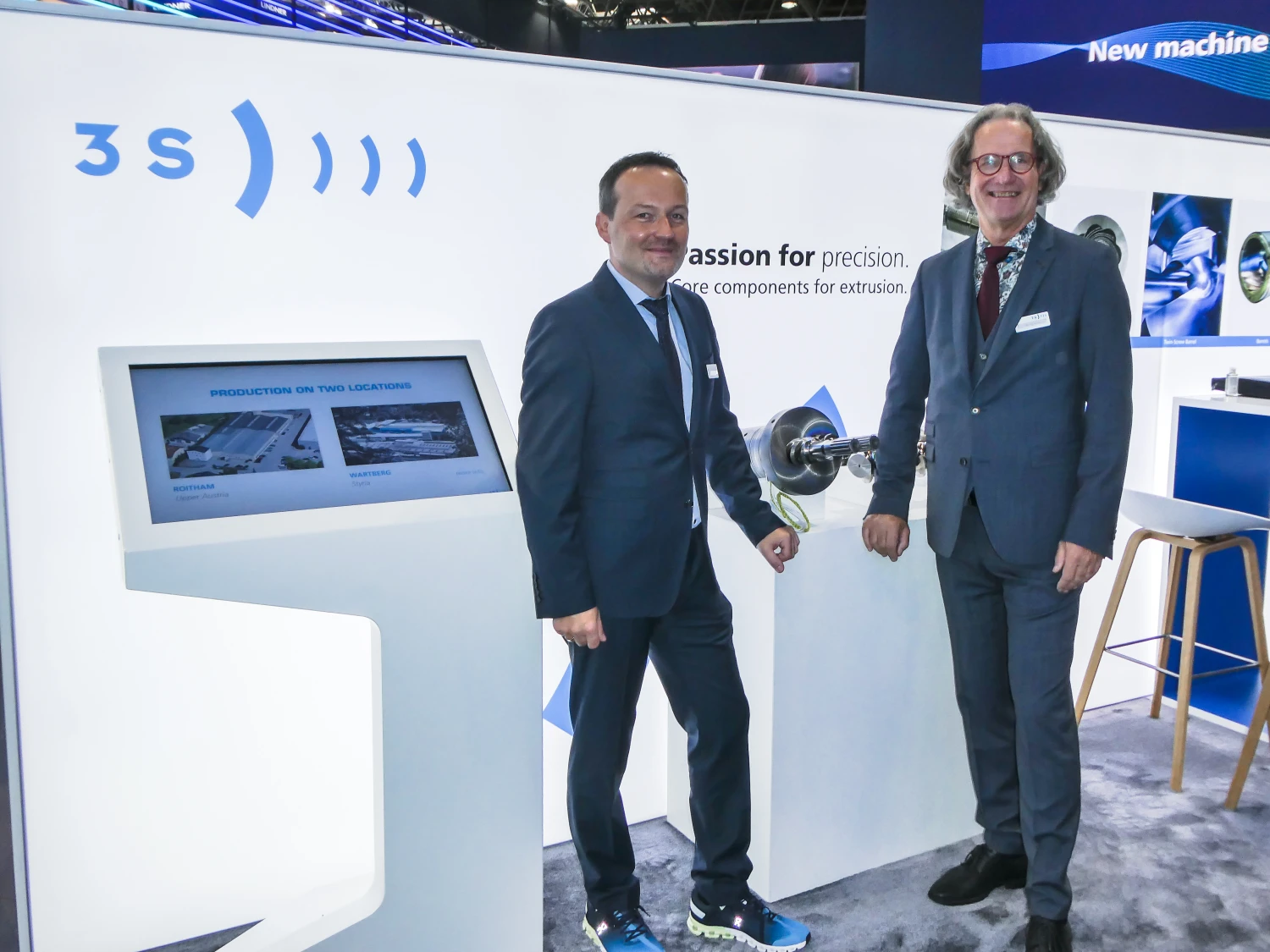
Karl Reisinger, Sales, und Alois Anreiter, Managing Director representing the company 3S at EREMA Group`s trade fair stand. Hall 9/C09
More efficient screw manufacturing without re-clamping
As another highlight, 3S will be demonstrating a new screw manufacturing technology. In a special machine, profile grinding can also be used to shape materials that would be too hard for conventional production methods. This allows the geometry and outer diameter of screws and other components to be ground in one go without re-clamping. Subsequent hardening treatment is no longer necessary. When the parts are removed from the machine they are finished and through-hardened. No final polishing is needed either. This technology is already being used in the production of discharge screws for Laserfilter 406, an EREMA filter system from the POWERFIL business unit, which will also be exhibited at the EREMA Group's trade fair stand.
Extrusion core parts form the basis for the circular economy
"Extruder screws consist of up to 30 parts, each of which is manufactured individually. We attach great importance to always being up to date in terms of our products as well as our production technology. This is the only way we can respond to each customer's needs and deliver long-lasting products," confirms Alois Anreiter. Customers also benefit from the know-how that 3S has acquired in other business areas over the past 30 years. "The components we manufacture are fundamental to processing plastic waste into high-quality recycled pellets. That is how we are also making an important contribution to the transition towards a circular economy," says Anreiter.
3S at K 2022
EREMA Group GmbH trade show stand: Halle 9, Stand C09
Download press release as .pdf:
Download Bild als .jpg:
Download Bild als .jpg: